What role does laser welding play in battery production for electric vehicles?
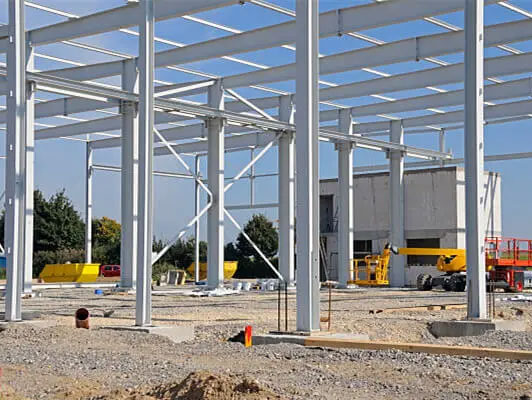
Introduction: Transforming EV Battery Manufacturing Through Laser Technology
The electric vehicle revolution has accelerated dramatically over the past decade, bringing with it unprecedented challenges and opportunities in battery manufacturing. As global automakers commit billions to electrification strategies, the demand for high-performance, safe, and cost-effective battery production solutions has never been greater. At the heart of this manufacturing evolution lies laser welding technology – a precision joining process that has become indispensable to modern EV battery production.
As specialists in advanced laser systems at DATO and Leapion, we've witnessed firsthand how laser welding has transformed battery manufacturing processes. The unique capabilities of laser welding address the critical challenges of EV battery production: creating reliable electrical connections, ensuring thermal management, maintaining structural integrity, and delivering the production speed necessary for commercial viability.
In this comprehensive exploration, we'll examine the multifaceted role that laser welding plays throughout the EV battery production process. From cell-level connections to pack-level integration, we'll detail how different laser welding technologies enable the precision, speed, and reliability demanded by electric vehicle manufacturers. Drawing on our extensive experience developing laser welding solutions for the EV industry, we'll provide insights into current best practices and emerging trends that are shaping the future of battery production.
The Fundamentals of EV Battery Architecture and Manufacturing Challenges
Understanding Battery Hierarchies and Connection Requirements
Before diving into specific laser welding applications, it's essential to understand the hierarchical structure of EV battery systems and the joining challenges they present. Modern electric vehicle batteries are complex assemblies organized in a hierarchy of components: individual cells combine to form modules, which in turn are integrated into complete battery packs that power the vehicle.
At the cell level, manufacturers typically employ cylindrical, prismatic, or pouch cell designs, each with distinct connection requirements. Cylindrical cells (like the 18650 or 21700 formats) require precise tab-to-terminal connections, while prismatic and pouch cells involve larger surface area connections between terminals and busbars. These connections must maintain extremely low electrical resistance while withstanding thermal cycling, vibration, and potential impact scenarios throughout the vehicle's operational life.
Module assembly introduces additional complexity, as multiple cells must be connected in series and parallel configurations to achieve desired voltage and capacity specifications. These connections often involve copper or aluminum busbars of varying thicknesses that must be joined to cell terminals without damaging the sensitive internal components of the cells. The thermal management systems integrated at this level further complicate the assembly process, requiring precise control of heat input during welding operations.
At the pack level, high-current connections between modules and to power distribution units demand robust joining methods that can handle substantial electrical loads while maintaining perfect reliability under automotive operating conditions. These connections often involve thicker materials and more complex geometries, pushing the capabilities of traditional joining methods to their limits.
Critical Manufacturing Challenges in Battery Production
The manufacturing challenges in EV battery production extend far beyond simply creating electrical connections. Battery manufacturers must simultaneously address multiple competing priorities that directly impact product performance, safety, and cost.
Electrical performance represents the most obvious requirement – connections must maintain extremely low resistance to minimize energy losses and heat generation during high-current charging and discharging cycles. Even small increases in connection resistance can significantly impact battery efficiency and thermal management requirements. Laser welding excels in this area by creating metallurgically bonded connections with minimal interface resistance.
Thermal management presents another critical challenge. Battery cells operate within narrow temperature ranges for optimal performance and safety, making heat control during the manufacturing process essential. Traditional welding methods often introduce excessive heat that can damage sensitive cell components or trigger thermal runaway events. Laser welding's precise energy control and localized heat input minimize this risk while still creating robust connections.
Production speed and scalability have become increasingly important as EV production volumes grow. Battery manufacturing facilities must produce thousands of connections per minute to meet production targets, requiring joining technologies that combine speed with reliability. The non-contact nature of laser welding, coupled with its ability to be easily automated and integrated into production lines, makes it ideally suited to high-volume battery manufacturing.
Quality assurance represents perhaps the most significant challenge in battery production. With hundreds or thousands of connections in a single battery pack, each one critical to performance and safety, manufacturers require joining processes that deliver consistent results with minimal defects. Advanced laser welding systems incorporate real-time monitoring capabilities that verify weld quality during production, enabling immediate detection and correction of process deviations.
Laser Welding Applications Across the Battery Production Chain
Cell-Level Connections: Precision at the Microscale
At the cell level, laser welding plays a crucial role in creating the initial electrical connections that form the foundation of battery performance. These applications demand extraordinary precision, with weld features often measured in fractions of a millimeter.
For cylindrical cells, tab welding represents one of the most common laser applications. This process joins the internal electrode tabs to the external terminal caps, creating the electrical pathway that allows the cell to function in a circuit. The challenge lies in creating a strong connection without penetrating too deeply into the cell, which could damage internal components or compromise seals. Pulsed laser welding systems excel in this application, delivering precisely controlled energy bursts that create strong connections with minimal heat-affected zones.
Prismatic cell terminal welding presents different challenges, often involving the joining of dissimilar materials like aluminum and copper. These connections must accommodate the different thermal expansion rates and electrical properties of the materials while maintaining perfect conductivity. Specialized laser welding techniques, including wobble welding patterns and beam oscillation, create wider weld seams that distribute stress and enhance long-term reliability under thermal cycling conditions.
Pouch cell tab sealing applications leverage laser welding's precision to create hermetic seals that prevent electrolyte leakage while maintaining electrical isolation between positive and negative terminals. These welds must be perfectly consistent along their entire length, with no gaps or weak points that could compromise cell integrity. Continuous wave fiber laser systems with precise beam shaping capabilities deliver the consistent energy distribution needed for these critical sealing operations.
Module-Level Integration: Balancing Speed and Precision
As cells are assembled into modules, laser welding continues to play a vital role in creating the electrical interconnections that define the module's performance characteristics. These applications typically involve larger components and higher production volumes, requiring welding solutions that balance precision with throughput.
Busbar welding represents one of the most common module-level applications, joining copper or aluminum conductors to cell terminals to create series and parallel connections. These connections must handle substantial current flows while accommodating the different thermal expansion rates of the materials involved. Scanner-based laser welding systems excel in this application, using galvanometer mirrors to rapidly direct the laser beam across multiple weld locations without moving the workpiece, dramatically reducing cycle times.
Terminal block connections join the module's external connection points to internal busbars, creating the interfaces through which the module connects to the broader battery system. These connections often involve thicker materials that challenge traditional welding methods. High-power fiber laser welding systems with multi-kilowatt capabilities can create deep penetration welds in these components while maintaining precise control of the heat-affected zone.
Cooling system integration often requires laser welding of thin-walled cooling plates or channels to module structures. These connections must be leak-tight while minimizing distortion that could affect thermal contact between cooling systems and cells. The precise energy control of laser welding creates strong, hermetic seals with minimal distortion, ensuring optimal thermal management performance throughout the module's operational life.
Pack-Level Assembly: Handling High-Power Connections
At the pack level, laser welding addresses the challenges of creating high-current connections between modules and to power distribution systems. These applications typically involve thicker materials and more complex geometries, pushing laser technology to deliver both power and precision.
High-current busbar welding joins the main power distribution elements of the battery pack, creating the pathways through which energy flows during charging and discharging. These connections must handle hundreds of amperes while maintaining minimal resistance and perfect reliability under automotive vibration and thermal cycling conditions. High-power laser welding systems, often with outputs exceeding 6kW, create deep penetration welds that ensure robust electrical and mechanical integrity.
Cooling manifold assembly often involves laser welding of aluminum components that form the pack's thermal management system. These welds must be perfectly leak-tight while accommodating the complex geometries typical of modern cooling system designs. The flexibility of fiber-delivered laser beams allows access to joints in confined spaces that would be inaccessible to traditional welding equipment, enabling more efficient cooling system designs.
Structural component integration leverages laser welding's ability to join dissimilar materials with minimal distortion. As battery packs increasingly serve as structural elements in vehicle designs, the ability to create strong, reliable joints between different materials becomes increasingly valuable. Advanced laser welding techniques, including hybrid laser-arc processes, enable joining of the high-strength steels and aluminum alloys commonly used in battery pack structures.
Advanced Laser Welding Technologies Enabling Battery Innovation
Specialized Laser Sources for Battery Applications
The diversity of joining challenges in battery production has driven the development of specialized laser sources optimized for specific applications. Understanding these technologies helps manufacturers select the optimal solution for each stage of the production process.
Continuous wave fiber lasers have become the workhorses of battery manufacturing, offering exceptional beam quality, reliability, and efficiency. These systems deliver consistent power output ideal for applications like busbar welding and terminal connections, where consistent penetration depth is critical. Modern fiber lasers offer power ranges from hundreds of watts to multiple kilowatts, with wall-plug efficiencies exceeding 30%, significantly reducing operating costs in high-volume production environments.
Pulsed laser systems deliver energy in precisely controlled bursts, making them ideal for applications where heat input must be minimized. These systems excel in delicate operations like tab welding on cylindrical cells, where excessive heat could damage internal components. Advanced pulsed lasers offer microsecond to nanosecond pulse durations with peak powers many times higher than their average output, creating strong welds with minimal heat-affected zones.
Green wavelength lasers operating at 532nm have emerged as valuable tools for welding highly reflective materials like copper, which are common in battery applications. While traditional infrared lasers at 1064nm can be reflected by clean copper surfaces, green wavelengths are more readily absorbed, enabling more efficient energy transfer and more consistent welding results. This technology has become increasingly important as battery designs incorporate more copper components for improved electrical performance.
Blue wavelength lasers (450nm) represent the cutting edge of battery welding technology, offering even better absorption characteristics for copper and gold-plated components. These systems enable welding of thinner materials with lower power levels, further reducing the risk of thermal damage to sensitive battery components. As battery designs continue to evolve toward higher energy densities, these specialized laser sources will play an increasingly important role in manufacturing.
Advanced Beam Delivery and Control Systems
The effectiveness of laser welding in battery production depends not only on the laser source but also on sophisticated beam delivery and control systems that ensure precision and consistency across thousands of welds.
Scanner-based welding systems use galvanometer mirrors to rapidly direct the laser beam across the workpiece, enabling multiple welds in quick succession without moving either the laser head or the part. These systems can execute complex weld patterns in milliseconds, dramatically reducing cycle times compared to mechanical positioning systems. Modern scanners offer positioning speeds exceeding 10 meters per second with positioning accuracies measured in microns, making them ideal for high-volume battery production.
Beam shaping technologies modify the energy distribution within the laser spot to optimize welding performance for specific materials and joint configurations. Techniques like beam splitting, ring-shaped profiles, and custom intensity distributions enable precise control of the melt pool dynamics, improving weld quality and process stability. These technologies are particularly valuable for welding dissimilar materials common in battery assemblies, where controlling the mixing ratio of different metals is critical to joint performance.
Real-time adaptive control systems monitor the welding process and make immediate adjustments to laser parameters based on feedback from sensors. These systems can detect and respond to variations in material properties, joint fit-up, and surface conditions, maintaining consistent weld quality despite normal manufacturing variations. Advanced systems incorporate multiple sensing technologies, including photodiodes, cameras, and spectroscopic analyzers, providing comprehensive insight into the welding process as it occurs.
Multi-beam approaches split the laser output into multiple spots that work simultaneously, enabling novel welding strategies for battery applications. Techniques like simultaneous welding of both sides of a busbar connection ensure balanced heat input and minimal distortion, while spatial beam splitting allows a single laser source to create multiple welds simultaneously, further increasing production throughput.
Quality Assurance in Laser Welded Battery Components
In-Process Monitoring for Zero-Defect Manufacturing
The safety-critical nature of EV batteries demands exceptional quality assurance measures throughout the production process. Modern laser welding systems incorporate sophisticated monitoring capabilities that verify weld quality in real-time, enabling immediate detection and correction of process deviations.
Photodiode-based monitoring systems track the intensity of light emissions from the welding process, providing immediate feedback on process stability. Deviations from established intensity patterns can indicate potential defects like porosity, lack of fusion, or excessive penetration. These systems operate at microsecond response times, enabling detection of defects as they form and even allowing for real-time process corrections in advanced systems.
High-speed camera monitoring captures visual images of the welding process at rates exceeding 10,000 frames per second, providing detailed information about melt pool dynamics and solidification patterns. Artificial intelligence algorithms analyze these images in real-time, identifying subtle indicators of potential quality issues before they become critical defects. This technology is particularly valuable for complex geometries and dissimilar material combinations common in advanced battery designs.
Spectroscopic analysis examines the wavelength distribution of light emitted during welding, providing insights into the metallurgical processes occurring in the weld pool. This technique can detect contamination, material variations, and even changes in shielding gas coverage that might affect weld quality. When integrated with process control systems, spectroscopic monitoring enables adaptive welding parameters that compensate for material variations in real-time.
Post-Process Verification and Traceability
While in-process monitoring provides immediate feedback on weld quality, comprehensive quality assurance systems also incorporate post-process verification methods that confirm the integrity of completed welds.
Electrical resistance testing measures the conductivity of completed connections, verifying that they meet the low-resistance requirements critical to battery performance. Automated systems can perform these measurements immediately after welding, identifying any connections that fall outside specified parameters for immediate rework. Advanced systems incorporate four-wire measurement techniques that eliminate contact resistance from the measurement, providing accurate resistance values in the micro-ohm range.
Mechanical testing assesses the structural integrity of welded connections through methods like pull testing, shear testing, and fatigue analysis. While typically performed on sample components rather than production parts, these tests provide valuable validation of process parameters and help establish correlation between in-process monitoring signals and actual weld strength. This correlation enables manufacturers to confidently rely on in-process monitoring for ongoing quality assurance.
X-ray and CT scanning technologies provide non-destructive evaluation of internal weld features that would otherwise be invisible. These techniques can detect subsurface defects like porosity, cracks, or incomplete fusion that might compromise long-term reliability. While typically too slow for 100% inspection in high-volume production, these methods are valuable for process validation and troubleshooting when integrated with statistical process control approaches.
Digital traceability systems tie all quality data together, creating comprehensive records for every battery component. Modern laser welding systems can generate unique identifiers for each weld, associating it with specific process parameters, monitoring data, and verification results. This digital thread enables complete traceability throughout the battery's lifecycle, from manufacturing through vehicle integration and even end-of-life recycling.
Future Trends in Laser Welding for EV Battery Production
Emerging Technologies Reshaping Battery Manufacturing
As electric vehicle technology continues to evolve, laser welding processes are advancing to meet new challenges and opportunities in battery production. Several emerging trends are reshaping the landscape of battery manufacturing.
Solid-state battery production represents one of the most significant upcoming challenges for laser welding technology. These next-generation batteries promise higher energy density and improved safety but introduce new materials and connection requirements. Laser welding systems are evolving to address these challenges, with specialized wavelengths and beam delivery systems optimized for the unique properties of solid-state battery components.
Multi-material battery designs are becoming increasingly common as manufacturers optimize for both performance and cost. These designs often incorporate aluminum, copper, nickel, and various specialized alloys within a single assembly, creating complex joining challenges. Advanced laser welding techniques like differential power distribution and controlled dilution enable reliable joining of these dissimilar materials while maintaining the specific properties required for each connection.
Miniaturization trends in battery design are pushing the limits of welding precision, with some connections now requiring sub-100-micron accuracy. Ultra-precise laser welding systems with advanced beam shaping capabilities are meeting this challenge, creating microscale connections with perfect reliability. These systems often incorporate adaptive optics that compensate for beam distortions, ensuring consistent focus quality even at the smallest scales.
Artificial intelligence integration is perhaps the most transformative trend in laser welding for battery production. AI systems analyze vast datasets from production processes to identify subtle patterns that human operators might miss, optimizing parameters for specific materials and joint configurations. Self-learning systems continuously improve over time, adapting to normal variations in materials and conditions to maintain consistent quality across millions of welds.
Sustainability and Circular Economy Considerations
As the electric vehicle industry matures, increasing attention is being paid to the full lifecycle environmental impact of battery production. Laser welding technologies are evolving to address these sustainability concerns.
Energy efficiency improvements in laser sources and beam delivery systems are reducing the carbon footprint of battery production. Modern fiber lasers offer wall-plug efficiencies exceeding 40%, dramatically reducing energy consumption compared to older laser technologies or conventional welding processes. These efficiency gains translate directly to lower carbon emissions and operating costs in high-volume manufacturing environments.
Design for disassembly is becoming an important consideration as manufacturers plan for end-of-life recycling of battery components. Laser welding systems are being developed that create connections strong enough for vehicle lifetime requirements while still allowing for controlled separation during recycling processes. Techniques like partial penetration welding and strategic joint design enable this balance between in-service strength and end-of-life separability.
Reduced material usage through precision joining is another sustainability benefit of advanced laser welding. By creating narrower, more precise connections, laser welding minimizes the amount of conductive materials required for electrical pathways. This reduction in copper and aluminum usage not only lowers material costs but also reduces the environmental impact associated with mining and refining these metals.
Process waste reduction is achieved through the non-contact nature of laser welding, which eliminates consumables like filler wires and fluxes required by many conventional welding processes. Additionally, the precise energy control of laser welding minimizes spatter and material loss during the joining process, further reducing waste streams in high-volume production environments.
Conclusion: Laser Welding as an Enabler of the Electric Vehicle Revolution
The transition to electric mobility represents one of the most significant industrial transformations of our time, with implications for energy systems, transportation infrastructure, and manufacturing processes worldwide. At the heart of this transformation lies the electric vehicle battery – a marvel of engineering that demands manufacturing precision beyond what was possible just a decade ago.
Laser welding technology has emerged as a critical enabler of this revolution, providing the precision, speed, and reliability necessary to produce batteries at the scale and quality level demanded by the automotive industry. From microscopic cell-level connections to robust structural joints in complete battery packs, laser welding processes create the foundation upon which electric vehicle performance and safety are built.
At DATO and Leapion, we're proud to contribute to this transformation through our advanced laser welding systems designed specifically for battery manufacturing applications. Our commitment to innovation drives continuous improvement in beam quality, process control, and monitoring capabilities, enabling battery manufacturers to achieve new levels of quality, throughput, and cost-effectiveness.
As the electric vehicle industry continues to evolve, laser welding technology will remain at the forefront of manufacturing innovation, enabling new battery designs, materials, and production processes. The journey toward sustainable transportation is just beginning, and we're excited to provide the laser welding solutions that will help make the electric future a reality.
Related Blogs
- Exploring the Safety, Precision, and Industrial Benefits of Laser Surface CleaningIn today’s fast-paced industrial world, where quality, efficiency, and sustainability are top priorities, manufacturers are constantly seeking better ways to clean metal surfaces without compromising material integrityBlog
- A Complete Guide by DATO and LeapionIn modern industry, surface preparation and maintenance play a crucial role in achieving high-quality manufacturing results. Laser cleaning machines have emerged as one of the most innovative, efficient, and environmentally friendly tools for removing contaminantsBlog
- Laser cleaning machines are revolutionizing industrial surface cleaning by offering a faster, safer, and more eco-friendly alternative to traditional methods. Whether removing rust, paint, oil, oxide, or other surface contaminants, laser cleaning has become a cutting-edge solution in manufacturing,Blog
- Introduction: Transforming EV Battery Manufacturing Through Laser TechnologyThe electric vehicle revolution has accelerated dramatically over the past decade, bringing with it unprecedented challenges and opportunities in battery manufacturing. As global automakers commit billions to electrificationBlog