Minimizing Porosity in Laser Welds: A Focus on Aluminum Alloys
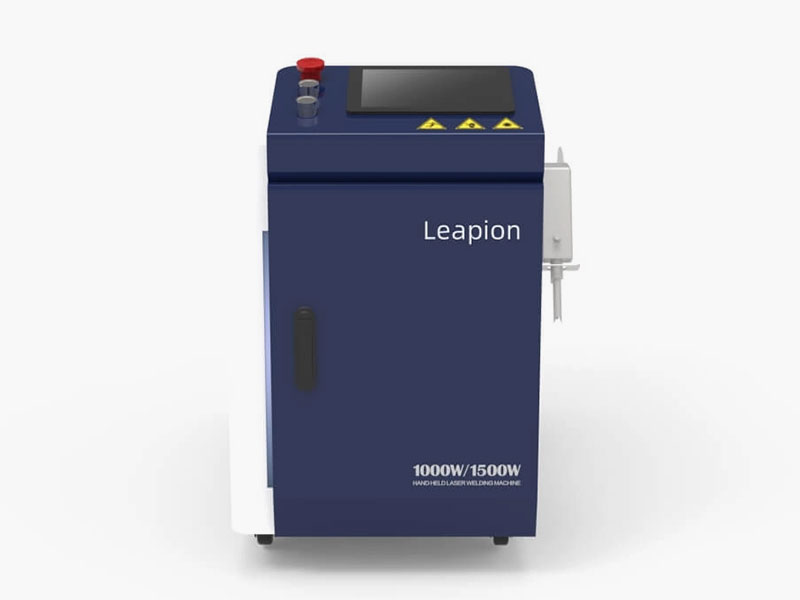
Laser welding offers numerous advantages in manufacturing, including precision, speed, and minimal heat-affected zones. However, one common challenge, particularly when welding aluminum alloys, is the formation of porosity within the weld. Porosity, which refers to the presence of voids or gas pockets within the weld metal, can significantly compromise the structural integrity and mechanical properties of the joint. At Dato and Leapion, we are dedicated to understanding and addressing these challenges, providing our customers with advanced laser welding solutions that minimize porosity and ensure high-quality welds. This article delves into the causes of porosity in laser welds, especially in aluminum alloys, and explores the optimization strategies that can be employed to mitigate this issue.
Understanding Porosity Formation in Laser Welding
Porosity in laser welds arises from the entrapment of gases within the molten weld pool as it solidifies. Several factors can contribute to this phenomenon, and understanding these factors is crucial for developing effective mitigation strategies.
Key Factors Contributing to Porosity
Gas Entrapment: The primary cause of porosity is the entrapment of gases within the molten metal. These gases can originate from various sources, including:
Shielding Gas: Improper shielding gas flow or contamination can lead to gas entrapment. Inadequate shielding can allow atmospheric gases to react with the molten metal, forming pores.
Material Contamination: Surface contaminants, such as moisture, oil, or oxides, can decompose during welding and release gases into the weld pool.
Dissolved Gases: Aluminum alloys often contain dissolved gases, such as hydrogen, which can be released during the rapid heating and cooling cycles of laser welding.
Keyhole Instability: In deep penetration laser welding, a keyhole is formed by the laser beam's intense energy. Instability in this keyhole can lead to gas entrapment and porosity. The keyhole can collapse prematurely, trapping gas and creating voids within the weld.
Rapid Solidification: The rapid cooling rates associated with laser welding can prevent gases from escaping the molten pool before solidification. This is particularly true for aluminum alloys, which have high thermal conductivity and solidify quickly.
Weld Pool Dynamics: The fluid flow within the molten weld pool can also contribute to porosity formation. Turbulent flow can trap gases and prevent them from escaping the weld.
Laser Parameters: Improper laser parameters, such as excessive laser power or welding speed, can exacerbate the formation of porosity. These parameters can influence the keyhole stability, heat input, and weld pool dynamics.
Material Properties: The inherent properties of the material being welded, such as its chemical composition, thermal conductivity, and melting point, can also affect the susceptibility to porosity formation. Aluminum alloys, with their high thermal conductivity and affinity for hydrogen absorption, are particularly prone to porosity.
Specific Challenges with Aluminum Alloys
Aluminum alloys present unique challenges when it comes to laser welding and porosity formation. Their high thermal conductivity, high reflectivity to common laser wavelengths, and strong affinity for hydrogen absorption make them more susceptible to porosity than other metals.
Why Aluminum Alloys are Prone to Porosity
High Thermal Conductivity: The high thermal conductivity of aluminum alloys leads to rapid heat dissipation, making it difficult to maintain a stable molten pool and allowing gases to become trapped. The rapid cooling rates also hinder the escape of gases before solidification.
High Reflectivity: Aluminum alloys are highly reflective to commonly used laser wavelengths, making it challenging to efficiently couple the laser energy into the material. This can lead to unstable keyhole formation and increased porosity.
Hydrogen Absorption: Aluminum alloys have a strong affinity for hydrogen absorption, particularly in the molten state. Hydrogen can be released during welding, forming pores within the weld.
Oxide Formation: Aluminum readily forms an oxide layer on its surface, which can trap moisture and other contaminants. These contaminants can decompose during welding, releasing gases that contribute to porosity.
Low Boiling Point of Alloying Elements: Some alloying elements in aluminum alloys have low boiling points, and they can vaporize during welding, leading to gas entrapment and porosity.
Optimizing Laser Welding to Reduce Porosity in Aluminum Alloys
To minimize porosity in laser welds, especially in aluminum alloys, it is crucial to carefully control the welding process and optimize various parameters. At Dato and Leapion, we are committed to providing our customers with the knowledge and technology to achieve high-quality, porosity-free welds.
Strategies for Porosity Reduction
Shielding Gas Optimization: Proper shielding gas selection and flow rate are critical for preventing atmospheric contamination and reducing porosity. Argon, helium, or mixtures of these gases are commonly used for welding aluminum alloys. The gas flow should be sufficient to protect the weld pool but not so high that it creates turbulence.
Surface Preparation: Thoroughly cleaning the material surface before welding is essential to remove contaminants that can contribute to porosity. This includes removing oxides, moisture, oil, and other foreign substances.
Laser Parameter Optimization: Precise control over laser parameters, such as laser power, welding speed, and focal spot size, is crucial for minimizing porosity. These parameters should be optimized based on the specific material and welding application.
Laser Power: Using the optimal laser power is essential to achieve sufficient penetration without causing excessive heat input or keyhole instability.
Welding Speed: Adjusting the welding speed can influence the heat input and weld pool dynamics, affecting the formation of porosity.
Focal Spot Size: The focal spot size can be adjusted to control the energy density and keyhole formation.
Beam Shaping: Advanced beam shaping techniques can be used to optimize the energy distribution and improve weld pool stability. This can include using a donut-shaped beam or a dual-beam system to reduce porosity.
Pulse Shaping: Using pulsed laser welding can help to control the heat input and reduce the risk of porosity. Pulsed lasers allow for better control over the weld pool dynamics and reduce the time for gases to become trapped.
Preheating: Preheating the material before welding can reduce the temperature gradient and minimize the risk of porosity. This is particularly beneficial for aluminum alloys, which have high thermal conductivity.
Filler Material Addition: Adding filler material during laser welding can improve the weld's mechanical properties and reduce porosity. The filler material can act as a deoxidizer and help to remove gases from the weld pool.
Vacuum Welding: Welding in a vacuum environment can significantly reduce porosity by eliminating atmospheric gases. This technique is particularly useful for high-precision applications.
Real-Time Monitoring and Control: Implementing real-time monitoring and feedback systems can help to detect and correct deviations in the welding process, ensuring consistent weld quality and minimizing porosity. This includes monitoring parameters such as laser power, welding speed, and weld pool temperature.
Optimized Joint Design: Designing the joint with specific geometries can improve the weld's strength and reduce the risk of porosity. This includes using bevels, grooves, or other joint preparations to facilitate deeper penetration and better fusion.
Hydrogen Removal: Implementing processes to remove hydrogen from the aluminum alloy before welding can significantly reduce the risk of porosity. This can be achieved through vacuum degassing or other specialized treatments.
Dato and Leapion's Laser Welding Solutions for Porosity Reduction
At Dato and Leapion, we are committed to providing our customers with advanced laser welding solutions that minimize porosity and ensure high-quality welds. Our laser welding machines are designed with advanced features and capabilities to address the specific challenges of welding aluminum alloys.
Dato and Leapion's Laser Welding Machine Features
Advanced Laser Sources: Our laser welding machines are equipped with high-quality laser sources that provide precise control over laser parameters, enabling optimal welding conditions for aluminum alloys.
Precise Beam Shaping: Our machines offer advanced beam shaping capabilities, allowing for optimized energy distribution and improved weld pool stability.
Real-Time Monitoring: Our machines feature real-time monitoring systems that track key welding parameters, ensuring consistent weld quality and minimizing porosity.
Customizable Solutions: We offer customizable laser welding solutions tailored to the specific needs of our customers, including the selection of optimal laser parameters, shielding gases, and process controls.
Expert Support: Our team of experienced engineers and technicians provides expert support to our customers, from initial consultation to installation and training. We are committed to ensuring that our customers achieve the best possible results with our laser welding machines.
Conclusion: Achieving Porosity-Free Laser Welds in Aluminum Alloys
While porosity remains a significant challenge in laser welding, particularly with aluminum alloys, it can be effectively minimized through careful process optimization and the use of advanced laser welding technologies. At Dato and Leapion, we are dedicated to providing our customers with the knowledge and tools they need to achieve high-quality, porosity-free welds. By understanding the underlying causes of porosity and implementing the appropriate mitigation strategies, manufacturers can unlock the full potential of laser welding for a wide range of applications. Our commitment to innovation and customer satisfaction ensures that our laser welding machines are at the forefront of technology, enabling our customers to achieve superior results.
Related Blogs
- Exploring the Safety, Precision, and Industrial Benefits of Laser Surface CleaningIn today’s fast-paced industrial world, where quality, efficiency, and sustainability are top priorities, manufacturers are constantly seeking better ways to clean metal surfaces without compromising material integrityBlog
- A Complete Guide by DATO and LeapionIn modern industry, surface preparation and maintenance play a crucial role in achieving high-quality manufacturing results. Laser cleaning machines have emerged as one of the most innovative, efficient, and environmentally friendly tools for removing contaminantsBlog
- Laser cleaning machines are revolutionizing industrial surface cleaning by offering a faster, safer, and more eco-friendly alternative to traditional methods. Whether removing rust, paint, oil, oxide, or other surface contaminants, laser cleaning has become a cutting-edge solution in manufacturing,Blog
- Introduction: Transforming EV Battery Manufacturing Through Laser TechnologyThe electric vehicle revolution has accelerated dramatically over the past decade, bringing with it unprecedented challenges and opportunities in battery manufacturing. As global automakers commit billions to electrificationBlog