Laser Welding Precision: Which Industries Benefit Most?
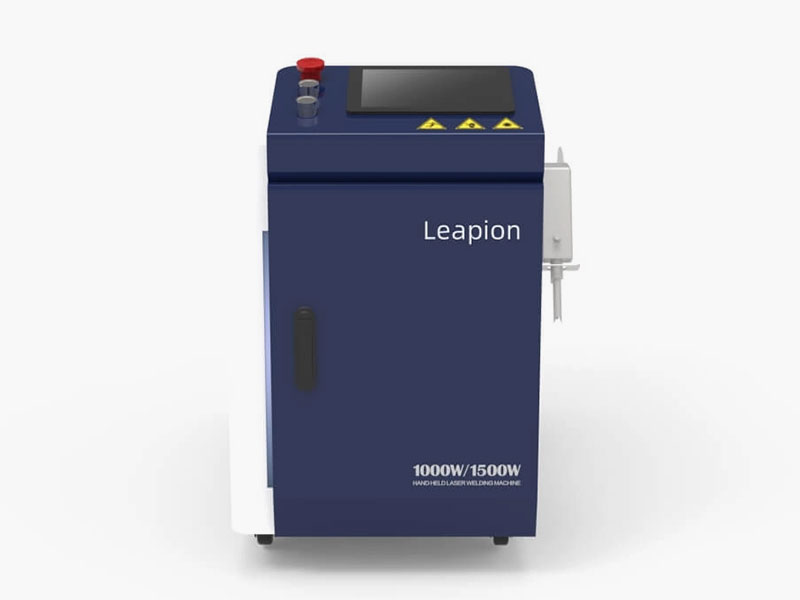
Introduction:
In modern manufacturing, precision isn't just a nice-to-have; it's the bedrock of quality, efficiency, and innovation. As industries push the boundaries of what's possible, laser welding has emerged as a transformative technology, offering unparalleled accuracy and control. For sectors where even the slightest deviation can have significant consequences, laser welding provides the reliability and consistency needed to thrive.
At DATO and Leapion, we've spent over 15 years empowering businesses with cutting-edge laser solutions. We specialize in providing innovative tools, including fiber laser cutting machines, tube laser cutting machines, sheet and tube laser cutting machines, laser welding machines, and laser cleaning machines. Our mission is to equip you with the technology you need to elevate productivity, enhance quality, and achieve unmatched precision.
This article will explore the industries that are reaping the greatest rewards from the precision of laser welding. We'll delve into how this technology is driving innovation and setting new standards across various sectors.
The Unmatched Precision of Laser Welding: What Sets It Apart?
Before we dive into specific industries, let's understand what makes laser welding so precise and why it's a superior alternative to traditional welding methods.
Laser welding harnesses the power of a highly focused laser beam to melt and join materials with extreme accuracy. The beam's narrow diameter allows for pinpoint control, enabling welds in tight, intricate, or otherwise inaccessible areas. This level of precision is simply unattainable with conventional methods.
Furthermore, laser welding minimizes heat input, significantly reducing the risk of warping, distortion, or damage to surrounding areas. The result is clean, consistent, and exceptionally high-quality welds.
Advanced automation and computer control systems further enhance precision, ensuring repeatability and consistency across large production runs. Whether you're joining thin sheets of metal or creating complex three-dimensional geometries, laser welding delivers results that meet and exceed the most demanding industry standards.
Industries Revolutionized: Who Benefits Most from Laser Welding Precision?
The precision of laser welding makes it an indispensable tool in industries where accuracy, reliability, and unwavering quality are paramount. Let's explore some of the key sectors that are experiencing a revolution thanks to this advanced technology:
Automotive Industry: Precision for Performance and Safety
The automotive industry is a major beneficiary of laser welding technology. From body panels and exhaust systems to critical engine components and advanced battery housings, laser welding ensures strong, durable, and aesthetically pleasing welds.
One of the key advantages of laser welding in automotive manufacturing is its ability to join dissimilar materials, such as high-strength steel and lightweight aluminum alloys. This is increasingly important in modern vehicles designed for weight reduction and improved fuel efficiency.
Moreover, the precision of laser welding minimizes heat-affected zones, reducing the risk of warping or distortion in thin materials. This is crucial for maintaining the structural integrity and aerodynamic performance of vehicle bodies.
As the industry transitions to electric vehicles (EVs), laser welding is playing a vital role in the manufacturing of battery packs, motor housings, and other critical components that demand high precision, reliability, and safety. Laser welding ensures the integrity of the battery enclosure, preventing leaks and protecting sensitive electronic components.
Aerospace Industry: Lightweight Strength for Critical Applications
The aerospace industry demands components that are exceptionally lightweight, incredibly strong, and capable of withstanding extreme conditions. Laser welding's precision and ability to join thin materials without distortion make it ideally suited for producing high-performance parts such as turbine blades, fuel nozzles, and critical airframe components.
Another significant advantage of laser welding in aerospace manufacturing is its ability to create smooth, defect-free welds. These flawless welds are essential for ensuring the structural integrity of aircraft and spacecraft, where even the smallest flaw can have catastrophic consequences. The technology's minimal heat input also reduces the risk of thermal stress, which can compromise the performance of advanced aerospace materials.
Electronics and Medical Devices: Reliability at a Microscopic Scale
In the electronics and medical device industries, precision is not just important; it's absolutely critical. Components are often incredibly small, remarkably delicate, and require intricate welds that traditional methods simply cannot achieve.
Laser welding is widely used in the production of sensors, microchips, and connectors, where even the slightest error can render the product unusable. Its ability to produce narrow, consistent welds ensures reliable electrical connections and minimizes the risk of damage to sensitive components.
In the medical device industry, laser welding is used to manufacture a wide range of instruments, implants, and diagnostic equipment. The technology's precision ensures that welds are clean, biocompatible, and free from contamination, meeting the stringent hygiene standards required in healthcare. Laser welding is used for creating hermetic seals in pacemakers and other implantable devices, ensuring their long-term reliability and safety.
Jewelry and Luxury Goods: Crafting Perfection with Light
The jewelry and luxury goods industry relies on laser welding for its ability to create seamless joins and intricate designs. Whether it's repairing delicate chains, setting precious gemstones, or crafting exquisite custom pieces, laser welding delivers results that are both beautiful and remarkably durable.
One of the standout features of laser welding in this industry is its ability to weld precious metals like gold, silver, and platinum without discoloration or distortion. This ensures that the final product retains its aesthetic appeal and intrinsic value. Laser welding allows jewelers to create intricate filigree designs and complex settings with unparalleled precision.
Energy and Power Generation: Strength and Reliability for Sustainable Solutions
In the energy sector, laser welding is used to manufacture components for renewable energy systems, such as high-efficiency solar panels and robust wind turbines. The technology's precision ensures that welds are strong, reliable, and capable of withstanding harsh environmental conditions.
Laser welding is also used in the production of critical nuclear reactor components, where safety and precision are of paramount importance. The ability to create defect-free welds ensures the long-term integrity of these components, minimizing the risk of failure and protecting the environment.
Tool and Die Manufacturing: Precision for Productivity
The tool and die industry requires precision welding for the production of molds, dies, and other essential components used in manufacturing processes. Laser welding's ability to create strong, consistent welds ensures that these tools meet the demanding standards required for high-volume mass production.
Moreover, laser welding can be used for repairing or modifying existing tools, extending their lifespan and significantly reducing production costs. Laser welding allows tool and die makers to create intricate cooling channels within molds, improving the efficiency of the molding process.
Consumer Appliances: Quality and Aesthetics for Everyday Products
In the production of consumer appliances like refrigerators, washing machines, and kitchen equipment, laser welding ensures that components are strong, durable, and aesthetically pleasing. The technology's precision allows for smooth, clean welds that enhance the overall quality and appearance of the final product. Laser welding is used to create seamless joints in stainless steel appliances, giving them a sleek and modern look.
Semiconductor Industry: Precision for Microscopic Components
The semiconductor industry relies on laser welding for assembling incredibly delicate components and ensuring reliable electrical connections. The technology's precision and minimal heat input protect sensitive materials from damage, making it an indispensable tool for this high-tech sector. Laser welding is used for creating connections in microelectronic circuits, ensuring their long-term reliability.
DATO and Leapion: Your Partner in Precision Laser Welding Solutions
At DATO and Leapion, we are dedicated to providing state-of-the-art laser welding machines that combine precision, unwavering reliability, and exceptional efficiency. Our machines are meticulously designed to meet the diverse needs of industries that demand the highest levels of accuracy and consistent quality.
Why Choose DATO and Leapion for Your Precision Laser Welding Needs?
Advanced Laser Welding Technology: Our laser welding machines incorporate the latest advancements in laser technology, delivering exceptional performance and unparalleled precision.
Custom Laser Welding Solutions: Whether you're working with incredibly thin sheets, complex three-dimensional shapes, or remarkably delicate materials, we offer tailored solutions to meet your specific requirements.
Compliance with Global Standards: Our machines meet major international standards like ISO9001, EU CE, and US FDA, ensuring safety, reliability, and peace of mind.
Unmatched Customer Support and Expertise: From initial installation to comprehensive after-sales service, our dedicated team is committed to providing unparalleled support to help you achieve your production goals.
Conclusion:
The precision of laser welding has revolutionized industries that demand accuracy, unwavering reliability, and exceptional quality. From automotive and aerospace to electronics and jewelry, laser welding is driving innovation and setting new standards for excellence.
At DATO and Leapion, we are proud to be at the forefront of this transformative technology, providing businesses with the tools they need to stay competitive in a rapidly evolving market.
If you're ready to experience the profound benefits of precision laser welding, we invite you to explore our comprehensive range of laser welding machines and discover how DATO and Leapion can help you achieve your manufacturing goals. Contact us today for a consultation and let us help you unlock the full potential of laser welding!
Related Blogs
- Exploring the Safety, Precision, and Industrial Benefits of Laser Surface CleaningIn today’s fast-paced industrial world, where quality, efficiency, and sustainability are top priorities, manufacturers are constantly seeking better ways to clean metal surfaces without compromising material integrityBlog
- A Complete Guide by DATO and LeapionIn modern industry, surface preparation and maintenance play a crucial role in achieving high-quality manufacturing results. Laser cleaning machines have emerged as one of the most innovative, efficient, and environmentally friendly tools for removing contaminantsBlog
- Laser cleaning machines are revolutionizing industrial surface cleaning by offering a faster, safer, and more eco-friendly alternative to traditional methods. Whether removing rust, paint, oil, oxide, or other surface contaminants, laser cleaning has become a cutting-edge solution in manufacturing,Blog
- Introduction: Transforming EV Battery Manufacturing Through Laser TechnologyThe electric vehicle revolution has accelerated dramatically over the past decade, bringing with it unprecedented challenges and opportunities in battery manufacturing. As global automakers commit billions to electrificationBlog