How does laser welding improve production speed and throughput?
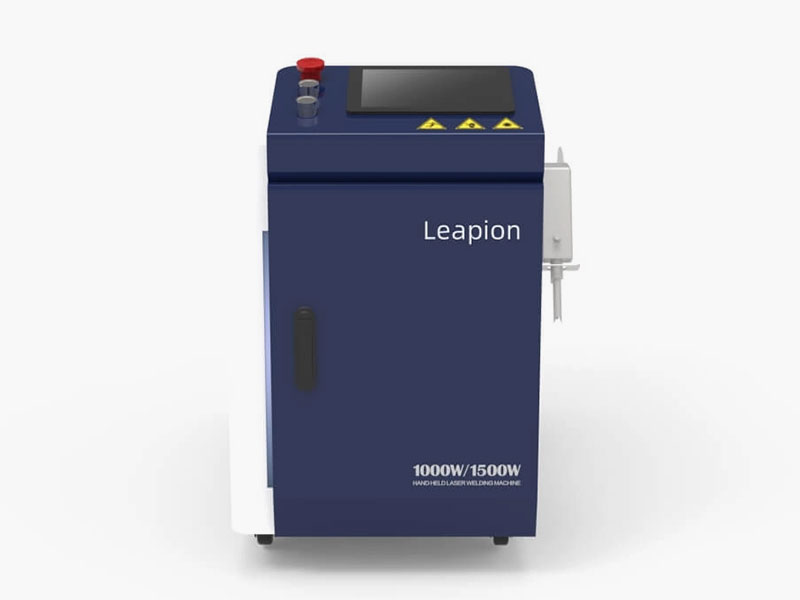
In the competitive landscape of modern manufacturing, efficiency is paramount. Companies are constantly seeking ways to optimize their production processes, reduce lead times, and increase output without compromising quality. Laser welding has emerged as a game-changing technology in this regard, offering significant advantages over traditional welding methods. For companies like DATO and Leapion, which specialize in advanced laser machines, understanding how laser welding enhances production speed and throughput is crucial for staying ahead in the industry.
The Fundamentals of Laser Welding
Laser welding is a high-precision welding technique that utilizes a focused laser beam to join materials. The laser beam delivers concentrated heat to a small area, allowing for rapid melting and solidification of the material. This process is characterized by its high energy density, minimal heat-affected zone, and ability to weld a wide range of materials, including metals, plastics, and composites.
The precision of laser welding enables manufacturers to achieve high-quality welds with minimal distortion, making it an ideal choice for applications where strength and aesthetics are critical. The technology's ability to work with various materials also makes it a versatile solution for different industries.
Key Advantages of Laser Welding in Production
High Welding Speed
One of the most significant benefits of laser welding is its ability to perform welds at exceptionally high speeds. Traditional welding methods, such as arc welding or gas welding, often require slower travel speeds to ensure proper fusion and avoid defects. In contrast, laser welding can achieve speeds several times faster due to its concentrated energy input. This rapid welding capability translates directly into increased production throughput, allowing manufacturers to complete more welds in less time.
The high welding speed not only enhances productivity but also enables manufacturers to meet tight deadlines and respond quickly to market demands. As a result, businesses can achieve a competitive edge in their respective industries.
Minimal Setup and Downtime
Laser welding systems are highly automated and require minimal setup time compared to traditional welding methods. The precision of the laser beam eliminates the need for extensive fixturing and alignment, reducing the time spent on preparation. Additionally, laser welding machines are designed for continuous operation with minimal maintenance, further minimizing downtime and maximizing production efficiency.
This reduction in setup time allows manufacturers to switch between different projects seamlessly, enhancing flexibility in production schedules. With the capability to quickly adapt to changing demands, companies can optimize their workflows and improve overall efficiency.
Consistent and High-Quality Welds
The precision of laser welding ensures consistent weld quality, even at high speeds. The focused laser beam produces clean, narrow welds with minimal spatter and distortion. This consistency reduces the need for post-weld processing, such as grinding or finishing, which can slow down production. High-quality welds also mean fewer defects and rework, contributing to overall production efficiency.
By minimizing the occurrence of defects, laser welding helps manufacturers maintain high-quality standards while reducing costs associated with rework and scrap materials. This reliability is particularly valuable in industries where quality control is critical.
Versatility in Material and Application
Laser welding is highly versatile and can be used on a wide range of materials, including metals, plastics, and composites. This versatility allows manufacturers to streamline their production processes by using a single welding method for multiple applications. For example, in the automotive industry, laser welding can be used for everything from body panels to engine components, reducing the need for multiple welding techniques and equipment.
This adaptability not only simplifies the production process but also enables manufacturers to reduce inventory costs associated with maintaining various welding machines. Companies can focus on their core competencies while leveraging the benefits of laser welding technology.
Integration with Automation
Laser welding is well-suited for integration with automated production lines. Robotic laser welding systems can be programmed to perform complex welds with high precision and repeatability. This automation not only increases production speed but also reduces labor costs and the potential for human error. In industries where high-volume production is essential, such as automotive and electronics, robotic laser welding systems are becoming increasingly common.
The integration of automation with laser welding technology allows manufacturers to achieve higher levels of efficiency and consistency. As production demands increase, the ability to automate welding processes becomes a crucial factor for maintaining competitiveness.
Real-World Applications of Laser Welding
Automotive Industry
In the automotive industry, laser welding is used extensively for body-in-white assembly, powertrain components, and battery manufacturing. The high speed and precision of laser welding enable automakers to produce vehicles more efficiently while maintaining strict quality standards. For example, laser welding is used to join aluminum and steel components in electric vehicle battery packs, ensuring strong, reliable connections that can withstand the rigors of daily use.
The automotive sector's increasing focus on lightweight materials and electric vehicles further emphasizes the importance of laser welding technology. As manufacturers strive to enhance fuel efficiency and reduce emissions, the ability to weld diverse materials becomes essential.
Electronics and Consumer Goods
The electronics industry benefits from laser welding's ability to join small, delicate components with high precision. In the production of smartphones, laptops, and other consumer electronics, laser welding is used to assemble components such as circuit boards, sensors, and connectors. The speed and accuracy of laser welding help manufacturers meet the high demand for these products while maintaining the quality and reliability expected by consumers.
As electronics continue to evolve, the miniaturization of components presents unique challenges. Laser welding technology provides solutions that enable manufacturers to create intricate designs without compromising functionality.
Medical Device Manufacturing
In the medical device industry, laser welding is used to assemble precision instruments, implants, and diagnostic equipment. The ability to weld small, complex components with minimal heat input is particularly valuable in this sector, where product integrity is critical. Laser welding ensures that medical devices are manufactured to the highest standards, with clean, strong welds that meet stringent regulatory requirements.
The medical industry’s focus on innovation and quality necessitates the use of advanced manufacturing techniques. Laser welding technology plays a vital role in ensuring that medical devices are safe, effective, and reliable.
The Future of Laser Welding in Manufacturing
As technology continues to advance, the capabilities of laser welding are expected to expand further. Innovations in laser sources, such as fiber lasers and ultrafast lasers, are enabling even higher welding speeds and greater precision. Additionally, advancements in automation and artificial intelligence are making laser welding systems more intelligent and adaptable, further enhancing their efficiency and versatility.
For companies like DATO and Leapion, staying at the forefront of these technological developments is essential. By investing in the latest laser welding technology and continuously improving their processes, they can offer their customers cutting-edge solutions that drive productivity and profitability.
Emphasizing Continuous Improvement and Innovation
To remain competitive, manufacturers must embrace continuous improvement and innovation. The integration of laser welding technology is just one aspect of a broader strategy to enhance production efficiency. By fostering a culture of innovation, companies can identify new opportunities for growth and stay ahead of industry trends.
Conclusion
Laser welding is transforming the manufacturing landscape by offering unparalleled speed, precision, and versatility. Its ability to perform high-quality welds at rapid speeds, coupled with minimal setup and downtime, makes it an invaluable tool for increasing production throughput. As industries continue to demand faster, more efficient production methods, laser welding will undoubtedly play a central role in meeting these challenges.
For DATO and Leapion, leveraging the power of laser welding is not just a competitive advantage—it is a pathway to sustained success in the global market. By embracing laser welding technology, manufacturers can achieve new levels of efficiency, quality, and innovation, ensuring they remain leaders in their respective industries. Whether in automotive, electronics, medical devices, or beyond, laser welding is the key to unlocking the full potential of modern manufacturing.
Related Blogs
- Exploring the Safety, Precision, and Industrial Benefits of Laser Surface CleaningIn today’s fast-paced industrial world, where quality, efficiency, and sustainability are top priorities, manufacturers are constantly seeking better ways to clean metal surfaces without compromising material integrityBlog
- A Complete Guide by DATO and LeapionIn modern industry, surface preparation and maintenance play a crucial role in achieving high-quality manufacturing results. Laser cleaning machines have emerged as one of the most innovative, efficient, and environmentally friendly tools for removing contaminantsBlog
- Laser cleaning machines are revolutionizing industrial surface cleaning by offering a faster, safer, and more eco-friendly alternative to traditional methods. Whether removing rust, paint, oil, oxide, or other surface contaminants, laser cleaning has become a cutting-edge solution in manufacturing,Blog
- Introduction: Transforming EV Battery Manufacturing Through Laser TechnologyThe electric vehicle revolution has accelerated dramatically over the past decade, bringing with it unprecedented challenges and opportunities in battery manufacturing. As global automakers commit billions to electrificationBlog