Exploring Material Compatibility: What Can You Weld with a Laser Welding Machine?
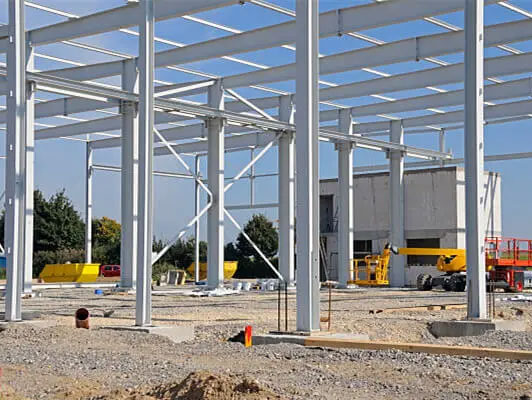
Laser welding has revolutionized manufacturing processes, offering unparalleled precision and efficiency in joining various materials. At Dato and Leapion, we understand that material compatibility is a key consideration when selecting a laser welding solution. This article will delve into the diverse range of materials that can be effectively welded using our advanced laser welding machines, highlighting the specific considerations for each material and exploring the possibilities for joining dissimilar metals. Whether you're working with common metals like stainless steel and aluminum or more specialized materials like titanium and copper, Dato and Leapion has the expertise and technology to meet your welding needs.
Dato and Leapion: Pioneering Excellence in Laser Welding Technology
Since 2007, Dato and Leapion has been at the forefront of the laser technology industry, consistently delivering high-quality and innovative solutions. Our commitment to research and development, combined with our extensive experience, enables us to provide laser welding machines that are not only powerful but also versatile. With a team of 500 skilled professionals, including 120 dedicated researchers, we continuously strive to improve our technologies and expand the range of materials that can be effectively welded. Our state-of-the-art manufacturing facility, coupled with our adherence to major international standards such as ISO9001, EU CE, and US FDA, ensures that our machines meet the highest levels of quality and reliability. This dedication to excellence is what makes Dato and Leapion a trusted partner for businesses seeking advanced laser welding solutions.
Understanding Laser Welding and Material Compatibility
Laser welding is a fusion welding process that uses a highly concentrated laser beam to melt and join materials together. The process is characterized by its high precision, minimal heat-affected zone (HAZ), and ability to weld a wide range of materials. However, not all materials are equally suitable for laser welding, and understanding the material properties and their interaction with laser energy is crucial for achieving optimal results. Factors such as melting point, thermal conductivity, reflectivity, and absorptivity play a significant role in determining the weldability of a material.
Common Metals Suitable for Laser Welding
Laser welding is particularly effective for joining a variety of common metals, each with its own specific considerations:
Stainless Steel Welding: Precision and Strength
Stainless steel is one of the most commonly welded materials using laser technology. Its high strength, corrosion resistance, and versatility make it a popular choice across various industries. Laser welding of stainless steel offers several advantages, including minimal distortion, high-quality welds, and precise control over the welding process.
Key Considerations for Laser Welding Stainless Steel:
Material Grade: Different grades of stainless steel have varying compositions and properties, which can affect weldability.
Shielding Gas: The use of appropriate shielding gases, such as argon or helium, is crucial to prevent oxidation and ensure a clean weld.
Laser Parameters: Precise control over laser power, welding speed, and focus is essential for achieving optimal results.
Applications of Laser Welding Stainless Steel:
Medical device manufacturing: Welding of surgical instruments and implants.
Food and beverage industry: Welding of processing equipment and storage tanks.
Automotive industry: Welding of exhaust systems and structural components.
Aerospace industry: Welding of aircraft components and engine parts.
Construction industry: Welding of architectural elements and structural supports.
If you are looking for a precise welding method for stainless steel, laser welding is an excellent choice. It allows for high-quality welds with minimal heat input, preserving the integrity and properties of the material.
Aluminum Welding: Lightweight and Efficient
Aluminum and its alloys are widely used in various industries due to their lightweight, corrosion resistance, and high strength-to-weight ratio. Laser welding of aluminum presents some challenges due to its high reflectivity and thermal conductivity, but with the right techniques and equipment, it can be effectively welded.
Key Considerations for Laser Welding Aluminum:
High Reflectivity: Aluminum reflects a significant portion of laser energy, requiring higher laser power and specialized techniques.
Thermal Conductivity: The high thermal conductivity of aluminum can lead to rapid heat dissipation, making it necessary to use higher welding speeds.
Shielding Gas: The use of argon or helium is crucial to prevent oxidation and porosity.
Laser Parameters: Precise control over laser power, welding speed, and focus is essential for achieving optimal results.
Applications of Laser Welding Aluminum:
Automotive industry: Welding of car bodies, engine components, and chassis.
Aerospace industry: Welding of aircraft structures and components.
Marine industry: Welding of boat hulls and marine equipment.
Electronics industry: Welding of electronic enclosures and heat sinks.
Packaging industry: Welding of aluminum packaging materials.
For those seeking a reliable method for welding aluminum, laser welding offers a precise and efficient solution. It is particularly useful for applications where lightweight and high-strength welds are required.
Carbon Steel Welding: Versatility and Strength
Carbon steel is a widely used material in various industries due to its strength, versatility, and cost-effectiveness. Laser welding of carbon steel offers several advantages, including high-speed welding, minimal distortion, and precise control over the welding process.
Key Considerations for Laser Welding Carbon Steel:
Material Grade: Different grades of carbon steel have varying compositions and properties, which can affect weldability.
Shielding Gas: The use of appropriate shielding gases, such as argon or carbon dioxide, is crucial to prevent oxidation and ensure a clean weld.
Laser Parameters: Precise control over laser power, welding speed, and focus is essential for achieving optimal results.
Applications of Laser Welding Carbon Steel:
Construction industry: Welding of structural steel components and frameworks.
Automotive industry: Welding of car bodies and chassis.
Manufacturing industry: Welding of machinery components and equipment.
Shipbuilding industry: Welding of ship hulls and structural elements.
Railroad industry: Welding of tracks and rail components.
If you need a strong and reliable welding method for carbon steel, laser welding is an excellent choice. It provides high-quality welds with minimal distortion, making it suitable for a wide range of applications.
Copper Welding: Challenges and Solutions
Copper and its alloys present unique challenges for laser welding due to their high reflectivity and thermal conductivity. However, with the right techniques and equipment, copper can be effectively welded using laser technology.
Key Considerations for Laser Welding Copper:
High Reflectivity: Copper reflects a significant portion of laser energy, requiring higher laser power and specialized techniques.
Thermal Conductivity: The high thermal conductivity of copper can lead to rapid heat dissipation, making it necessary to use higher welding speeds.
Shielding Gas: The use of argon or helium is crucial to prevent oxidation and porosity.
Laser Parameters: Precise control over laser power, welding speed, and focus is essential for achieving optimal results.
Applications of Laser Welding Copper:
Electronics industry: Welding of electrical connectors and components.
Automotive industry: Welding of electrical wiring and components.
Aerospace industry: Welding of electrical wiring and components.
Heat exchanger manufacturing: Welding of copper tubing and fins.
Art and sculpture: Creating intricate metal artwork.
For those seeking a precise method for welding copper, laser welding offers a solution that can overcome the challenges associated with this material. It is particularly useful for applications where high-precision and minimal heat input are required.
Titanium Welding: Strength and Lightweight
Titanium and its alloys are known for their high strength-to-weight ratio, corrosion resistance, and biocompatibility. Laser welding of titanium offers several advantages, including high-quality welds, minimal heat-affected zone, and precise control over the welding process.
Key Considerations for Laser Welding Titanium:
Reactivity: Titanium is highly reactive with oxygen and nitrogen, requiring the use of inert shielding gases.
Shielding Gas: The use of high-purity argon or helium is crucial to prevent contamination and ensure a clean weld.
Laser Parameters: Precise control over laser power, welding speed, and focus is essential for achieving optimal results.
Applications of Laser Welding Titanium:
Aerospace industry: Welding of aircraft components and engine parts.
Medical device manufacturing: Welding of surgical implants and instruments.
Chemical processing industry: Welding of corrosion-resistant equipment.
Marine industry: Welding of marine components and equipment.
Automotive industry: Welding of high-performance engine components.
If you need a reliable welding method for titanium, laser welding offers a high-precision and efficient solution. It is particularly useful for applications where high strength and corrosion resistance are required.
Welding Dissimilar Metals: Expanding Possibilities
Laser welding also offers the possibility of joining dissimilar metals, which can be challenging with traditional welding methods. However, careful consideration of material properties, melting points, and thermal expansion coefficients is crucial for achieving successful welds. The precise control offered by laser welding allows for the minimization of intermetallic compound formation, which can lead to brittle welds.
Key Considerations for Welding Dissimilar Metals:
Material Compatibility: Understanding the metallurgical compatibility of the metals being joined is essential.
Melting Points: Differences in melting points can lead to uneven melting and poor weld quality.
Thermal Expansion Coefficients: Differences in thermal expansion can cause stress and cracking in the weld.
Laser Parameters: Precise control over laser power, welding speed, and focus is crucial for achieving optimal results.
Filler Material: The use of appropriate filler materials can help to bridge the gap between dissimilar metals and improve weld quality.
Examples of Dissimilar Metal Welding with Laser Technology:
Steel to Aluminum: Commonly used in the automotive and aerospace industries.
Copper to Aluminum: Used in electrical and electronic applications.
Stainless Steel to Carbon Steel: Used in various industrial applications.
Titanium to Aluminum: Used in aerospace and medical applications.
Nickel Alloys to Stainless Steel: Used in high-temperature and corrosive environments.
Laser welding of dissimilar metals requires careful planning and execution, but it opens up a wide range of possibilities for creating complex and high-performance components. The ability to join different materials with precision and minimal heat input makes laser welding an invaluable tool for various industries.
Material Limitations in Laser Welding: Understanding the Boundaries
While laser welding is a versatile technique, it's important to acknowledge its limitations in terms of material compatibility. Some materials are inherently difficult to weld due to their properties, such as:
High Reflectivity: Materials like pure copper and gold can reflect a significant portion of laser energy, making them challenging to weld without specialized techniques.
High Thermal Conductivity: Materials with high thermal conductivity, such as aluminum and copper, can quickly dissipate heat, requiring higher laser power and faster welding speeds.
Low Melting Points: Materials with very low melting points can be prone to distortion and excessive melting during laser welding.
Reactive Metals: Some metals, such as magnesium and titanium, are highly reactive with oxygen and nitrogen, requiring the use of inert shielding gases and specialized welding techniques.
Non-Metals: Generally, laser welding is primarily used for joining metals. Welding of non-metals or polymers typically requires different laser technologies and processes.
Understanding these limitations is crucial for selecting the appropriate welding method and ensuring successful results. At Dato and Leapion, our team of experts can help you assess the weldability of your materials and recommend the best laser welding solution for your specific needs.
The Dato and Leapion Advantage: Expertise and Support You Can Rely On
Choosing Dato and Leapion as your laser welding machine supplier means partnering with a company that is committed to providing not only advanced technology but also comprehensive support and expertise. Our team of experienced engineers and technicians is dedicated to helping you achieve optimal results with our laser welding machines.
Key Advantages of Choosing Dato and Leapion:
Extensive Material Knowledge: We have a deep understanding of material properties and their interaction with laser energy.
Customized Solutions: We can tailor our laser welding solutions to meet your specific material requirements and application needs.
Comprehensive Training: We provide thorough training programs to ensure that your team can operate and maintain our machines effectively.
Ongoing Support: We offer reliable technical support and maintenance services to keep your machines running smoothly.
Innovation and Research: We are constantly pushing the boundaries of laser welding technology, ensuring that our customers have access to the latest advancements.
We are proud to be a leader in the laser technology industry, and our commitment to quality, innovation, and customer satisfaction is evident in every machine we produce. We understand that choosing the right laser welding solution is a critical decision, and we are here to guide you through the process and provide you with the best possible equipment and support.
Conclusion: Unlock the Potential of Laser Welding with Dato and Leapion
Laser welding offers a versatile and precise method for joining a wide range of materials, from common metals like stainless steel and aluminum to more specialized materials like titanium and copper. The ability to weld dissimilar metals further expands the possibilities for creating complex and high-performance components. At Dato and Leapion, we are dedicated to providing you with the most advanced laser welding solutions and the expertise you need to succeed.
Whether you are looking to weld stainless steel, aluminum, carbon steel, copper, titanium, or even dissimilar metals, Dato and Leapion has the right laser welding machine for your application. Our commitment to quality, innovation, and customer satisfaction ensures that you receive a reliable, high-performance laser welding solution that meets your needs and exceeds your expectations.
We encourage you to contact us today to discuss your specific material welding requirements and learn how Dato and Leapion can help you achieve your manufacturing goals. Our team of experts is ready to assist you in selecting the best laser welding solution for your business and provide you with the support you need to succeed.
Related Blogs
- Exploring the Safety, Precision, and Industrial Benefits of Laser Surface CleaningIn today’s fast-paced industrial world, where quality, efficiency, and sustainability are top priorities, manufacturers are constantly seeking better ways to clean metal surfaces without compromising material integrityBlog
- A Complete Guide by DATO and LeapionIn modern industry, surface preparation and maintenance play a crucial role in achieving high-quality manufacturing results. Laser cleaning machines have emerged as one of the most innovative, efficient, and environmentally friendly tools for removing contaminantsBlog
- Laser cleaning machines are revolutionizing industrial surface cleaning by offering a faster, safer, and more eco-friendly alternative to traditional methods. Whether removing rust, paint, oil, oxide, or other surface contaminants, laser cleaning has become a cutting-edge solution in manufacturing,Blog
- Introduction: Transforming EV Battery Manufacturing Through Laser TechnologyThe electric vehicle revolution has accelerated dramatically over the past decade, bringing with it unprecedented challenges and opportunities in battery manufacturing. As global automakers commit billions to electrificationBlog